Water-cooled stone cutting gives you superior results by continuously removing heat through coolant circulation, preventing thermal damage and cracks in expensive materials. You’ll experience extended blade life since water reduces friction and strain on cutting tools while eliminating hazardous silica dust for safer working conditions. The technology delivers unmatched precision with minimal chipping, cleaner cuts, and reduced material waste. You’ll also benefit from lower operating costs and enhanced productivity. Continue exploring to discover the complete advantages.
The Science Behind Water-Cooled Cutting Technology
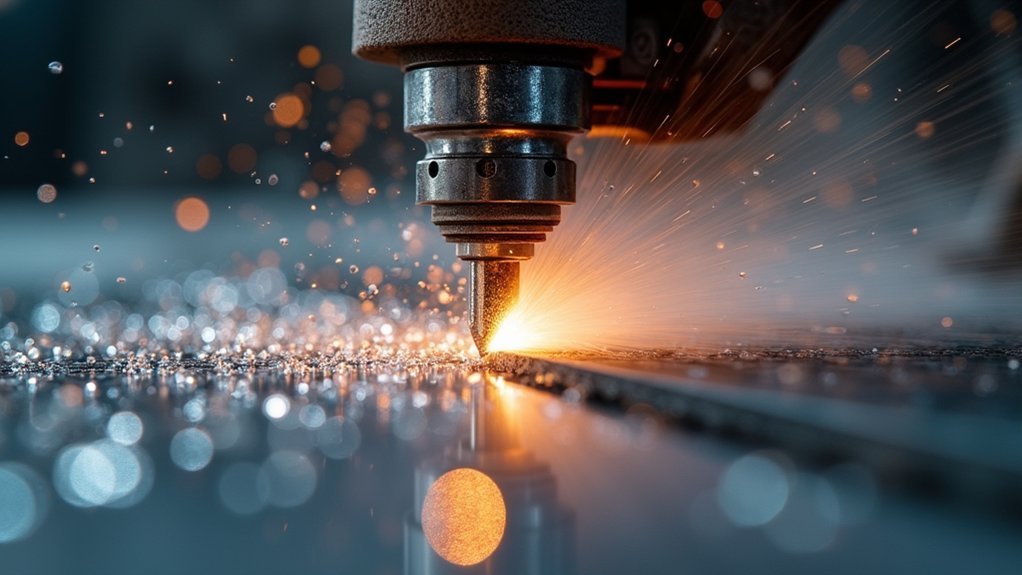
When you cut stone without proper cooling, the intense friction generates tremendous heat that can destroy your tools and crack the material.
Water-cooled cutting technology solves this problem by continuously removing heat through coolant circulation, preventing thermal damage to both your cutting tools and stone surfaces.
The science is straightforward: water acts as both a coolant and lubricant, dramatically reducing friction between your blade and the stone.
This dual function enhances your cutting performance by maintaining ideal operating temperatures while simultaneously flushing away debris and stone particles that would otherwise interfere with the cut.
Proper coolant flow and concentration are critical for managing heat buildup during high-speed operations, preventing thermal cracks and extending tool life while delivering cleaner, more precise cuts.
Heat Reduction and Temperature Control Benefits
When you implement water-cooled stone cutting technology, you’ll immediately notice how it prevents thermal cracks that can ruin your expensive stone materials.
The consistent temperature control doesn’t just protect your workpiece—it dramatically extends your cutting tool’s lifespan by preventing heat-induced wear and degradation.
You’re fundamentally getting double protection: safeguarding both your investment in materials and your cutting equipment through effective heat management.
Thermal Crack Prevention
Although stone cutting generates intense heat that can compromise both your material and tools, water-cooled systems effectively manage these thermal challenges by continuously dissipating heat at the cutting point.
You’ll find that this constant cooling prevents thermal cracks from forming in sensitive materials like marble, granite, and engineered stone. When temperatures spike during cutting operations, materials expand unevenly, creating stress points that lead to fractures.
Water cooling maintains ideal temperature ranges throughout the process, eliminating these dangerous thermal fluctuations. You’ll notice that your cuts remain clean and precise without the characteristic spider-web patterns or hairline fractures that plague dry cutting methods.
This protection becomes especially critical when working with expensive or irreplaceable stone materials.
Extended Tool Lifespan
Beyond protecting your stone materials, water cooling dramatically extends the lifespan of your cutting tools by maintaining ideal operating temperatures throughout demanding cutting operations.
You’ll notice that water-cooled blades maintain their sharpness and hardness considerably longer than dry-cutting alternatives. This temperature control prevents the thermal stress that typically causes premature tool wear and degradation.
When you use water cooling, you’re reducing the frequency of blade replacements, which translates to substantial cost savings over time.
The consistent cooling prevents your tools from overheating, which would otherwise dull cutting edges and compromise their structural integrity.
This extended tool lifespan means you’ll experience improved cutting efficiency throughout each blade’s operational life, making water-cooled stone cutting a smart investment for both performance and economics.
Enhanced Blade Life and Performance

Three critical factors determine your blade’s lifespan during stone cutting operations: heat management, friction reduction, and material stress.
Water-cooled cutting systems address each of these elements to deliver enhanced blade life that considerably outperforms dry cutting methods.
When you use water cooling, you’re actively dissipating heat that would otherwise cause thermal damage to your blade edges. The coolant reduces friction between blade and material, minimizing strain while boosting cutting efficiency.
This combination prevents premature wear patterns that typically shorten tool life.
- Prevents chipping and cracking in both blade and stone materials
- Enables ideal cutting speeds without compromising blade integrity
- Reduces electrical current consumption during operations
You’ll achieve cleaner cuts, improved finish quality, and faster completion times while maximizing your blade investment.
Precision and Clean Cut Quality
You’ll achieve superior precision with water-cooled cutting because the heat-free technology eliminates thermal expansion that can throw off measurements.
The constant water flow minimizes material chipping by reducing friction and clearing debris from your cut line instantly.
You’ll notice dramatically enhanced edge accuracy since there’s no heat-induced warping or stress that typically compromises traditional cutting methods.
Heat-Free Cutting Technology
When waterjet technology cuts through stone, it eliminates heat generation entirely, preserving your material’s original microstructure and preventing thermal damage that traditional cutting methods can’t avoid.
This heat-free cutting technology maintains your stone’s integrity and strength throughout the entire operation, ensuring you don’t compromise the material’s natural properties.
Without heat or surface stress, you’ll experience these key advantages:
- Enhanced material utilization – Minimal kerf reduces waste and maximizes your yield
- Superior edge quality – Virtually no chipping eliminates the need for additional hand finishing
- Complex design capability – Intricate patterns like waterfall countertops cut with precision and speed
This technology markedly boosts your productivity compared to traditional methods while delivering consistently clean results that preserve your stone’s structural integrity.
Minimal Material Chipping
Water-cooled stone cutting technology delivers exceptional precision by maintaining ideal temperatures that prevent the thermal stress responsible for material chipping. You’ll notice dramatically cleaner cuts with smoother edges when water minimizes friction between the blade and stone during the cutting process.
Cutting Method | Chipping Level | Edge Quality | Design Capability |
---|---|---|---|
Dry Cutting | High | Rough | Limited |
Water-Cooled | Minimal | Smooth | Advanced |
Waterjet | Virtually None | Premium | Intricate |
Standard Wet | Moderate | Good | Standard |
Waterjet cutting achieves virtually no chipping on edges, even for thin materials, thanks to its controlled precision. You can create intricate designs like waterfall countertops with minimal chipping, enhancing your project’s aesthetic quality. Advanced cooling mechanisms effectively manage heat generation, preserving stone integrity throughout the entire cutting process.
Enhanced Edge Accuracy
Because water-cooled cutting systems eliminate heat build-up, they deliver edge tolerances markedly tighter than traditional dry methods can achieve.
When you’re working with stone, thermal deformation from heat can throw off your measurements and compromise your project’s precision. Water cooling prevents this issue entirely, maintaining your material’s structural integrity throughout the cutting process.
Enhanced edge accuracy becomes possible through several key mechanisms:
- Continuous debris removal – Water flushes away particles that would otherwise interfere with cutting precision
- Zero thermal stress – No heat means no expansion or warping during cuts
- Consistent cutting conditions – Stable temperatures maintain uniform performance
You’ll notice smoother edges with less chipping when using water-cooled systems.
This superior precision allows you to execute intricate designs like waterfall countertops with minimal kerf, ensuring your finished product meets exact specifications.
Dust Suppression and Workplace Safety
Although traditional dry cutting methods generate hazardous silica dust clouds that pose serious respiratory risks, water-cooled stone cutting dramatically transforms workplace safety by suppressing airborne particles at their source.
You’ll experience remarkable dust suppression as water encapsulates particles before they become airborne, maintaining cleaner air quality throughout your cutting operations. This wet environment enhances visibility by clearing debris from your work area, enabling more accurate cuts while reducing accident risks.
Safety Aspect | Dry Cutting | Water-Cooled Cutting |
---|---|---|
Dust Generation | High silica exposure | Minimal airborne particles |
Visibility | Obscured by dust clouds | Clear, unobstructed view |
Respiratory Risk | Significant health hazards | Dramatically reduced exposure |
Slip Hazards | Dusty, slippery surfaces | Controlled wet conditions |
Regulatory Compliance | Challenging to maintain | Easier adherence to standards |
You’ll find compliance with occupational safety regulations becomes straightforward when dust levels consistently meet workplace air quality guidelines.
Material Preservation and Reduced Chipping
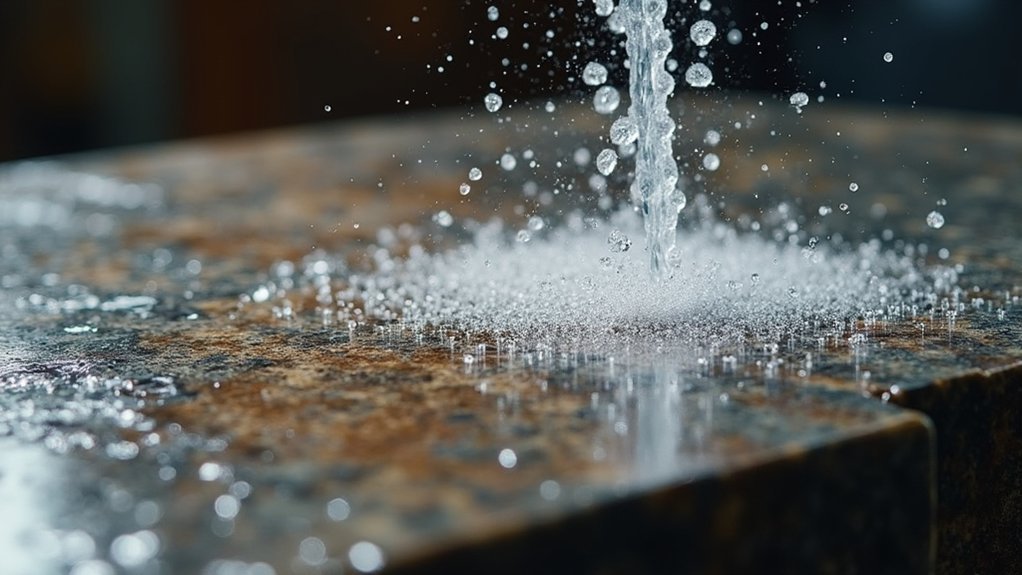
When you use water-cooled cutting methods, you’ll maintain a heat-free process that prevents thermal stress from damaging your stone’s internal structure.
You’ll notice markedly less chipping and edge damage because the water acts as both a coolant and lubricant, creating cleaner, more precise cuts.
This approach lets you retain the stone’s original strength and aesthetic qualities while achieving the intricate designs that would be impossible with traditional dry cutting techniques.
Heat-Free Cutting Process
While conventional stone cutting generates excessive heat that can compromise material integrity, water-cooled cutting systems maintain ideal temperatures throughout the process.
You’ll experience superior results when you implement this heat-free cutting process, as it prevents thermal damage that typically occurs with traditional methods.
The water cooling system offers several key advantages:
- Temperature control – Coolant dissipates heat effectively, maintaining consistent cutting conditions
- Friction reduction – Water lubrication creates smoother tool movement and cleaner cuts
- Microstructure preservation – Heat-free environment protects the stone’s internal composition
You’ll find that this controlled environment greatly reduces the risk of chipping and cracking, particularly when working with delicate materials like sintered stone.
The consistent temperature maintenance guarantees your finished surfaces achieve superior aesthetic quality while preserving material integrity.
Minimal Edge Damage
Because water-cooled cutting systems eliminate thermal stress, you’ll achieve remarkably clean edges with minimal chipping or material damage.
Water acts as a protective barrier, reducing friction between your cutting tool and stone surface. This friction reduction prevents the micro-fractures that typically cause edge deterioration in traditional cutting methods.
Water-cooled cutting technology delivers superior results, especially with delicate materials where precision matters most.
You’ll notice dramatically less waste since the cutting process preserves more usable material from each stone slab. The continuous cooling prevents thermal expansion that often leads to stress fractures along cut lines.
When you’re working on intricate designs or thin materials, minimal edge damage becomes essential for project success.
Water-cooled systems maintain consistent temperatures throughout the cutting process, ensuring your edges remain smooth and intact.
Original Strength Retention
Beyond preserving edge quality, water-cooled cutting technology maintains the original strength and structural integrity of your stone materials. The controlled temperature environment prevents thermal stress that can weaken stone at the molecular level.
You’ll find that your cut pieces retain their inherent durability and performance characteristics.
Water-cooled systems deliver superior original strength retention through several key mechanisms:
- Heat dissipation – Coolants effectively remove generated heat, preserving the stone’s natural microstructure
- Thermal crack prevention – Controlled temperatures minimize deformation and stress fractures that compromise material integrity
- Structural preservation – The cooling effect maintains the stone’s original composition without thermal degradation
This preservation approach guarantees your stone maintains its engineered properties, resulting in superior long-term performance and reliability in your applications.
Debris Removal and Cutting Zone Maintenance
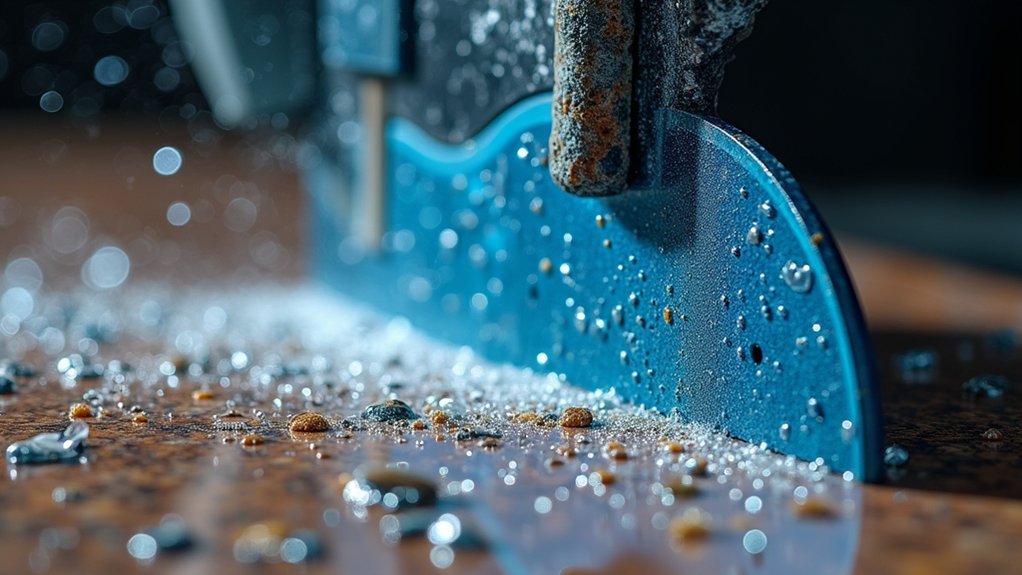
As water flows across the cutting surface, it carries away stone particles and metal filings that would otherwise accumulate and compromise your cut quality. This continuous debris removal prevents particles from welding to cutting surfaces due to heat buildup. When swarf and debris aren’t properly flushed away, they create scratches, reduce cutting efficiency, and damage your tools.
Without Water Cooling | With Water Cooling | Result |
---|---|---|
Debris accumulates | Particles flushed away | Clean cuts |
Heat welding occurs | Suspended particles | Smooth operation |
Surface smearing | Reduced friction | Quality finish |
Tool clogging | Clear cutting zone | Extended tool life |
Water cooling maintains ideal cutting conditions by keeping your work zone clean, ensuring consistent performance and professional results every time.
Optimal Flow Rates and Water Pressure Settings
While effective cooling depends on maintaining clean cutting zones, achieving ideal performance requires precise control of your water flow rates and pressure settings.
Getting these parameters right makes the difference between professional results and costly mistakes.
For peak flow rates, you’ll want to maintain 3 to 5 gallons per minute during cutting operations. This range guarantees effective cooling while removing debris efficiently from your work surface.
- Maintain water pressure between 40-60 psi to assure consistent coolant flow and prevent overheating
- Monitor flow rates regularly to improve cutting efficiency and reduce blade wear, saving you money
- Adjust settings based on stone type to enhance performance and preserve material integrity
This precise control minimizes thermal cracks by effectively dissipating heat, prolonging your tool life considerably.
Cost Efficiency and Material Waste Reduction
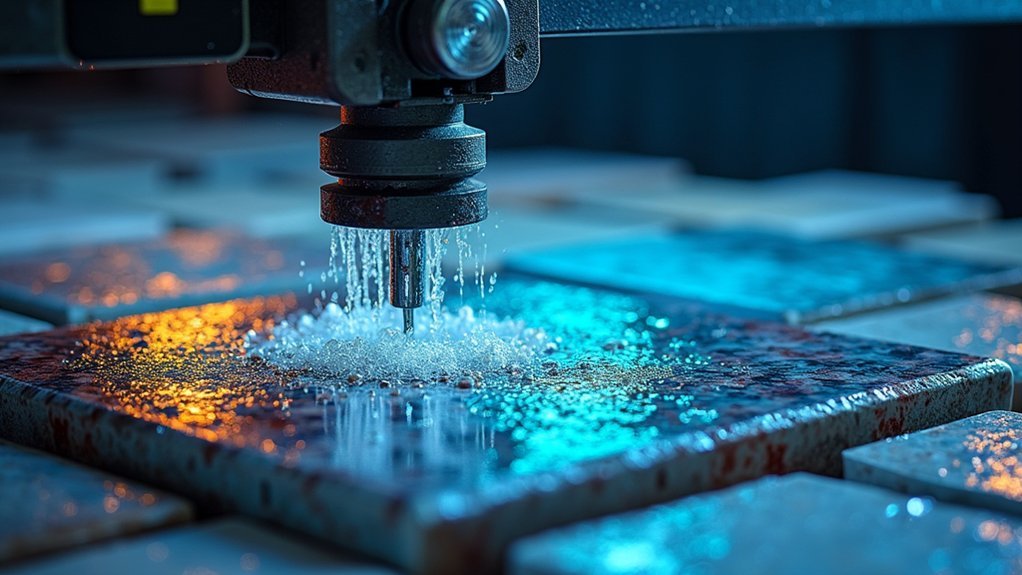
When you implement water-cooled stone cutting systems, you’ll immediately notice considerable reductions in material waste and operational costs.
Waterjet technology’s minimal kerfs notably improve material utilization while reducing raw material expenses. You’ll experience fewer rejected pieces since complex designs cut without breakage, directly lowering production costs.
The technology eliminates virtually all edge chipping, reducing your need for hand finishing and saving significant labor costs on post-processing.
Businesses like Atlanta Natural Stone demonstrate this cost efficiency through considerable raw material savings and increased productivity. You’ll complete intricate projects like waterfall counters two to three times faster than traditional methods.
This enhanced efficiency speeds up your production timeline and provides better cost control, making waterjet cutting financially advantageous for custom-built home projects.
Professional Results in Custom Stone Applications
Professional contractors and custom stone fabricators consistently achieve superior results through water-cooled cutting systems that deliver unmatched precision for high-end applications.
You’ll find that water-cooled cutting transforms complex projects like waterfall countertops and intricate architectural elements into manageable tasks while preserving material integrity.
When you’re working with premium granite and marble, water-cooled cutting guarantees you maintain the stone’s original appearance and structural strength.
The technology prevents thermal damage that could compromise your finished product’s quality.
- Enhanced Speed and Precision: Waterjet technology cuts complex designs two to three times faster than traditional methods
- Superior Surface Quality: Water coolant reduces surface stress and prevents chipping on delicate materials
- Luxury Market Standards: Flow Waterjet systems meet growing demand for bespoke stone finishes in high-end homes
Frequently Asked Questions
Why Do You Cut Stone With Water?
You cut stone with water because it cools your cutting tool, prevents overheating and cracks, lubricates the blade, flushes away debris, reduces chipping, and creates smoother, cleaner cuts.
Can Water Cut Through Rock?
You can cut through rock with water using high-pressure jet technology. When you pressurize water over 60,000 psi, it’ll penetrate granite and marble while preserving structural integrity without heat damage.
In Summary
You’ll find water-cooled stone cutting delivers unmatched precision while protecting your investment in blades and equipment. The technology eliminates heat damage, reduces dust hazards, and guarantees clean cuts every time. You’re getting superior results with less waste, extended tool life, and a safer work environment. When you’re working with valuable stone materials, water-cooled cutting isn’t just an option—it’s the professional standard that assures quality outcomes.
Leave a Reply