You’ll master fundamental skills like reading facet diagrams, operating handpiece-style machines, and developing material-specific polishing techniques during stone faceting apprenticeship training. The all-encompassing program covers essential equipment selection, workspace setup, precise rough analysis, and advanced cutting methods for various gemstones. You’ll learn proper angle calculations, quality assessment techniques, and how to avoid common issues like windowing while developing muscle memory for consistent results. Discover the complete breakdown of skills and equipment you’ll need to succeed.
Understanding the Fundamentals of Stone Faceting
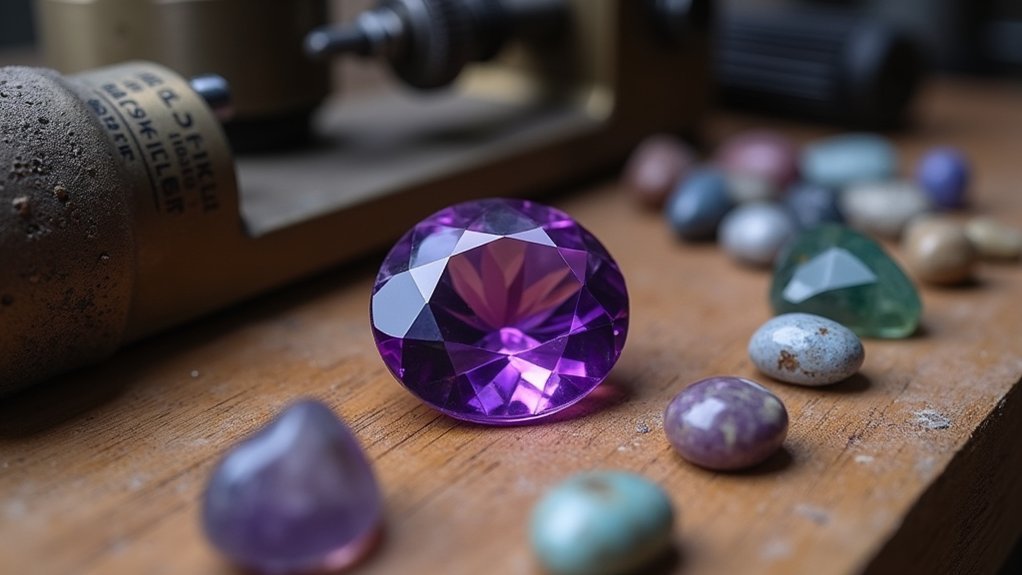
When you begin stone faceting apprenticeship training, you’ll first master the fundamentals on handpiece-style machines, starting with basic rough cutting techniques before advancing to complex recutting methods.
You’ll learn to read facet diagrams, which serve as blueprints for precise gemstone cutting. Hand preforming becomes essential as you shape rough stones before the detailed faceting process begins.
Your faceting setup requires understanding machine components and proper positioning for best results.
You’ll develop skills in material-specific polishing techniques, recognizing that different gemstones demand unique approaches.
The training emphasizes analyzing rough gemstones to understand their properties and potential, ensuring you make informed cutting decisions.
Through hands-on practice with various stones, you’ll build foundational knowledge while beginning to develop your personal cutting style and technique preferences.
Essential Equipment and Tool Requirements
Your success in stone faceting depends on acquiring the right equipment from the start.
Proper equipment selection at the beginning determines whether your faceting journey leads to frustration or mastery of this precise craft.
You’ll need a faceting machine with a speed controller for precise cutting control during your training. A handpiece with a cheater feature is recommended for better functionality, though non-cheater versions work too.
Your complete fasteners tool kit should include a cutting board, red dot wax, tweezers, and an alcohol burner for the dopping station.
Essential polishing equipment includes an 8-inch bat lap and Dominatrix lap, plus additional laps for specific stones.
Don’t overlook these vital accessories: a digital scale for accurate measurements, calipers for precision, oil and diamond powder for slurry preparation, and a gooseneck light for ideal visibility throughout the cutting process.
Setting Up Your Dedicated Workspace
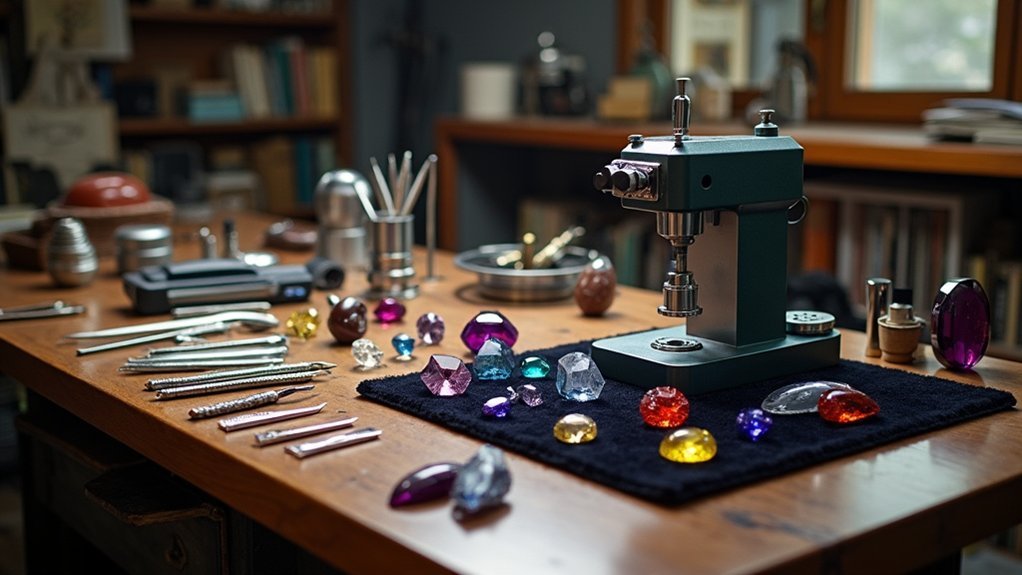
You’ll need to establish a well-organized workspace that accommodates your faceting machine, proper lighting system, and thorough tool kit for successful stone cutting.
Your setup should include essential equipment like a gooseneck light for visibility, a 96 index gear in jprim style for precision, and an all-inclusive dopping station with all necessary accessories.
Investing in quality components from the start will streamline your workflow and create an ideal learning environment throughout your apprenticeship training.
Essential Equipment Requirements
Setting up a dedicated workspace marks the foundation of your faceting journey, and you’ll need an extensive equipment list to participate effectively in the apprenticeship program.
Your essential equipment requirements begin with a complete faceting machine featuring a speed controller and handpiece, preferably with a cheater feature for enhanced functionality.
Beyond the machine itself, you’ll need thorough tools for successful gem preparation and cutting:
- Complete dopping station with cutting board, red dot wax, tweezers, and alcohol burner
- Digital scale, calipers, loops, and glue for precise measurements and securing
- Diamond powder for slurry creation and oil for lubrication
- Polishing laps including 8-inch bat lap and Dominatrix lap for finishing
- Organized 96 index gear in jprim style for accuracy and efficiency
Workspace Organization Tips
A well-organized workspace transforms chaotic faceting sessions into smooth, efficient operations where every tool has its designated place and purpose.
Your studio setup should center around your faceting machine with speed controller and handpiece, ideally featuring a cheater function for precision work. Organize tools around a 96 index jprim style system to minimize errors and streamline your process.
Position your complete dopping station nearby, including cutting board, red dot wax, tweezers, and alcohol burner for efficient stone preparation.
Install proper gooseneck lighting to illuminate intricate details during cutting.
These workspace organization tips include storing acetone in glass jars and keeping diamond slurry in small, accessible containers.
This systematic approach guarantees smooth workflow and reduces time wasted searching for essential tools.
Tool Kit Components
Success in stone faceting depends heavily on assembling the right tool kit components that’ll support your apprenticeship journey from basic cuts to advanced polishing techniques.
You’ll need a complete dopping station featuring a cutting board, red dot wax, tweezers, and alcohol burner for proper stone preparation. Your faceting machine should include a speed controller model with a handpiece featuring a cheater function for enhanced control.
Essential tool kit components include:
- Digital scale and precise calipers for accurate measurements
- Alcohol spray bottle with specialized loops for cleaning
- High-quality glue and oil for stone mounting
- Diamond powder for creating effective slurry mixtures
- Gooseneck light providing ideal workspace illumination
You’ll also need polishing laps, specifically an 8-inch bat lap and Dominatrix lap, purchased separately for course completion requirements.
Mastering Handpiece Techniques and Machine Operation
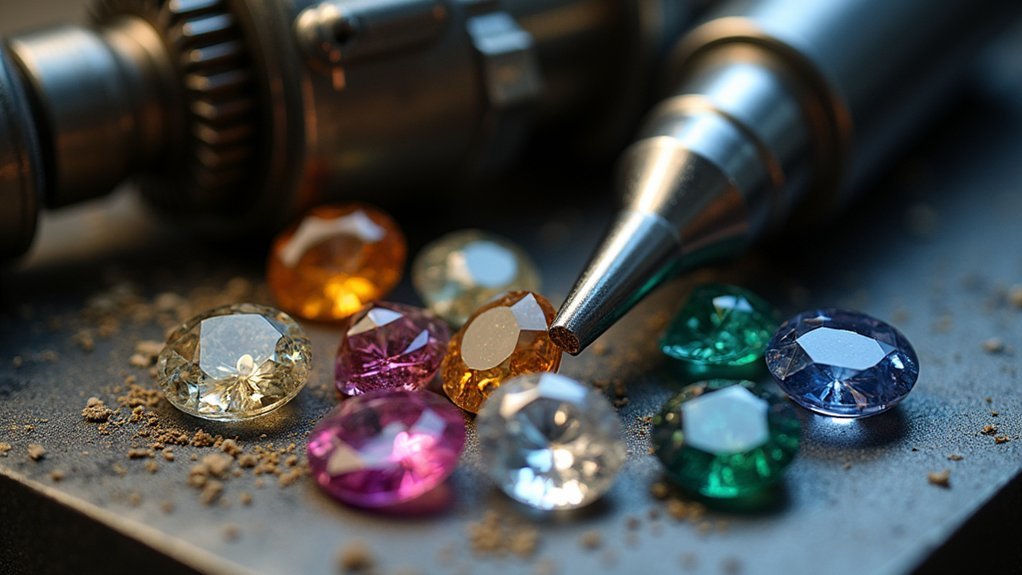
Mastering the handpiece transforms your raw cutting potential into precise, professional results. During apprenticeship training, you’ll learn essential techniques that separate amateur work from professional gemstone faceting. The cheater feature becomes your secret weapon for enhanced control during delicate cutting operations.
Machine Component | Key Technique | Quality Impact |
---|---|---|
Handpiece Control | Steady pressure application | Consistent facet angles |
Setup Calibration | Precise angle adjustments | Accurate gem proportions |
Maintenance Protocol | Regular cleaning cycles | Extended equipment life |
Your training emphasizes proper machine maintenance and setup procedures that guarantee peak performance throughout each cutting session. You’ll develop muscle memory for handpiece positioning while learning to read facet diagrams accurately. This foundation enables you to execute both classic symmetrical designs and complex non-symmetrical patterns with confidence and precision.
Polishing Methods and Lap Selection
Once you’ve mastered handpiece control and machine operation, the quality of your gemstone’s final appearance depends entirely on your polishing technique and lap selection.
During your apprenticeship, you’ll learn to use specialized laps for different stages and stone types. The Dominatrix lap handles pre-polishing and polishing tasks, while lightning laps and copper laps target specific gemstone varieties. You’ll work with oxide sticks and a bat stick sharpener to achieve professional-grade finishes.
Essential polishing methods include:
- Using an 8-inch bat lap for consistent results during frequent classroom practice
- Applying the dark side lap with oxides for enhanced quartz and emerald clarity
- Selecting appropriate lap materials based on gemstone hardness and composition
- Maintaining proper oxide application techniques for brilliant surface finishes
- Sourcing quality equipment from Gearloose for reliable training materials
Reading and Interpreting Facet Diagrams
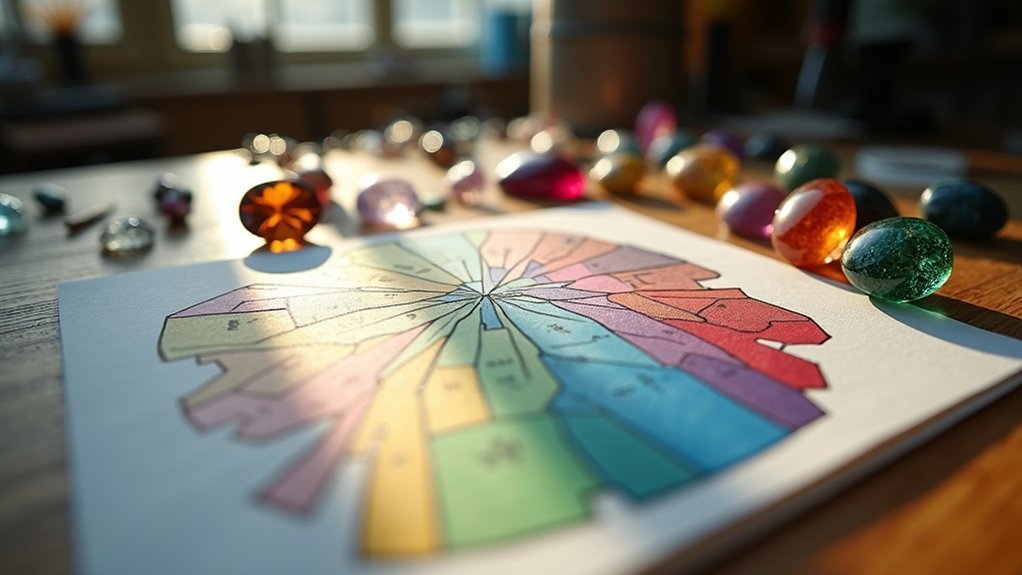
While polishing transforms your rough stone into a brilliant gem, you’ll need to master facet diagrams to achieve consistent, professional results.
Reading facet diagrams requires understanding each facet’s angles, sizes, and positions that create the desired design and brilliance. You’ll interpret various diagram types, from classic symmetrical patterns to complex non-symmetrical designs, enabling you to replicate existing cuts or develop innovative styles.
Precise measurements on these diagrams aren’t suggestions—they’re critical for accurate cutting and ideal light performance.
You’ll learn to recognize specialized symbols and notations that indicate specific cutting techniques for each facet. Many gemology programs at GIA emphasize this essential skill because mastering facet diagram interpretation directly impacts your finished gem’s quality and aesthetic appeal.
Material-Specific Cutting and Polishing Approaches
Different gemstone materials demand distinct cutting and polishing approaches because each stone’s hardness, crystal structure, and optical properties create unique challenges during fabrication.
You’ll master material-specific polishing techniques that address each gemstone’s unique requirements, using specialized laps and polishing agents to achieve superior surface quality.
Through thorough rough analysis training, you’ll learn to evaluate each stone’s potential and determine ideal cutting strategies that maximize yield and brilliance.
The program emphasizes calibrated sizing methods to achieve precise dimensions across different materials while teaching you essential techniques for avoiding windows that compromise a stone’s visual appeal.
- Diamond powder creating mirror-like surfaces on hard garnets
- Cerium oxide revealing sapphire’s deep blue fire
- Tin oxide bringing out tourmaline’s electric colors
- Careful angle adjustments preventing quartz from windowing
- Strategic rough positioning maximizing emerald’s natural beauty
Precision Measurement and Calibrated Sizing
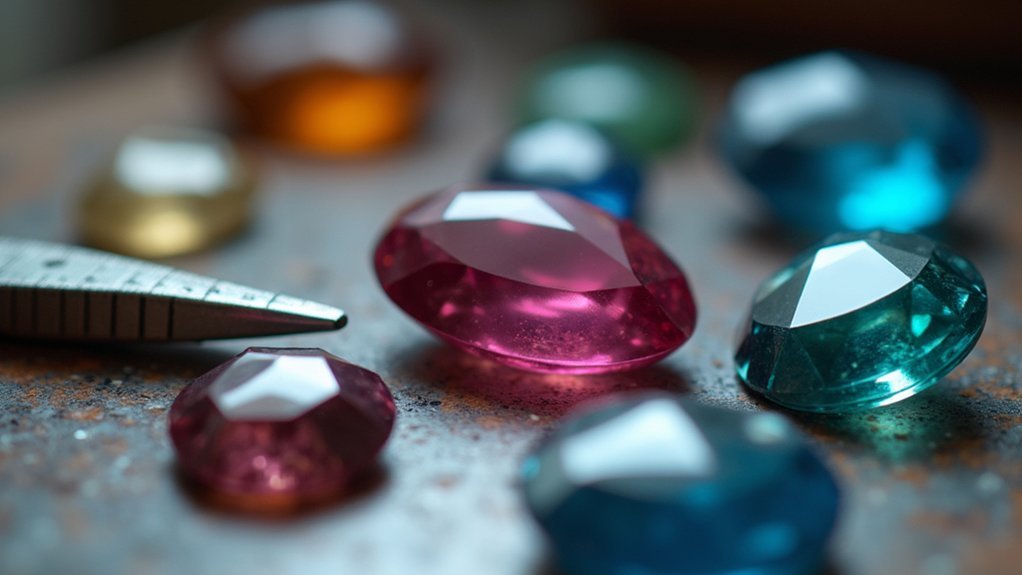
Mastering these material-specific techniques requires unwavering precision in measurement and calibrated sizing to transform your polished stones into marketable gems.
You’ll learn to use essential tools like calipers and digital scales to guarantee accurate dimensions throughout the faceting process. Calibrated sizing becomes vital when creating stones for specific settings, requiring you to understand industry standards and measurement techniques.
Precision measurement tools and calibrated sizing techniques ensure your faceted stones meet exact industry standards for professional jewelry settings.
Your training emphasizes measuring angles and proportions to achieve desired optical effects and aesthetic appeal.
You’ll master reading facet diagrams that provide detailed specifications for cutting angles and sizes, assuring consistency in your work. Additionally, you’ll learn techniques for adjusting and maintaining faceting machine settings, allowing you to produce stones with exact measurements tailored to your intended design specifications.
Advanced Techniques for Mixed Cuts and Recutting
Twenty-nine detailed lessons guide you through the complex art of combining traditional and contemporary cutting styles in mixed cuts and recutting applications.
You’ll master advanced techniques that transform rough stones into extraordinary gemstone designs through software-planned precision cutting. The curriculum emphasizes rough analysis skills, teaching you to identify ideal materials for recutting projects while avoiding common pitfalls like windowing.
- Analyzing rough crystal formations under magnification to determine ideal cutting orientations
- Programming faceting machines with precise angle calculations for seamless style changes
- Calibrating gemstones to exact millimeter specifications for jewelry setting requirements
- Maintaining cutting equipment with specialized oils and alignment tools for consistent performance
- Blending brilliant and step-cut faceting patterns to create distinctive light reflection zones
You’ll develop expertise in machine maintenance protocols that guarantee peak performance throughout complex cutting sequences.
Quality Assessment and Window Avoidance
Successful completion of mixed cuts depends entirely on your ability to evaluate gemstone quality and prevent windowing throughout the cutting process.
During your apprenticeship, you’ll master quality assessment techniques that examine clarity, color, and cut precision to guarantee ideal brilliance and sparkle. Window avoidance becomes critical as you learn to identify transparent areas that diminish a stone’s appearance through careful angle calculations.
Mastering quality assessment and window avoidance through precise angle calculations ensures your gemstones achieve maximum brilliance and sparkle.
You’ll study facet diagrams that guide precise angle placement, enhancing light reflection while minimizing unwanted transparency.
Your training includes analyzing rough stones before cutting, understanding how material shape and inclusions affect final results.
Throughout your apprenticeship, ongoing assessments of polished stones develop your eye for quality, enabling you to make real-time adjustments that perfect your cuts and eliminate windows.
Ongoing Support and Skill Development Resources
While mastering mixed cuts requires initial training, your true expertise develops through consistent access to ongoing support and skill development resources that extend far beyond your apprenticeship completion.
The online program provides unlimited access to instructional videos covering foundational through advanced techniques. You’ll repeat purchased courses indefinitely without additional costs, ensuring continuous skill development through practice and refinement.
Extensive resources like “The Secret Teachings of Gemcutting” offer cutting diagrams and in-depth knowledge supporting your ongoing learning journey.
- Watching advanced faceting demonstrations frame by frame to perfect your technique
- Accessing cutting diagrams that guide you through complex geometric patterns
- Connecting with experienced instructors who provide personalized feedback on your work
- Participating in community discussions about troubleshooting challenging stones
- Receiving regular updates introducing innovative cutting methods and industry developments
Frequently Asked Questions
Is Gem Faceting Difficult?
You’ll find gem faceting challenging because it requires precise cutting and polishing skills, understanding complex angles, and extensive practice. The steep learning curve demands patience, but continuous repetition helps you master these intricate techniques.
How Much Do Gem Cutters Make?
You’ll earn around $30,000 starting out as a gem cutter, but experienced cutters make $70,000+ annually. Freelancers charge $50-150 per hour, with specialized custom work commanding considerably higher rates.
What Is the Easiest Gemstone to Facet?
You’ll find quartz is the easiest gemstone to facet. It’s affordable, has good hardness at 7 on the Mohs scale, and its clarity helps you spot mistakes easily while learning cutting techniques.
How to Become a Gemstone Cutter?
You’ll need to enroll in specialized courses like an Online Apprenticeship Program, acquire a complete faceting setup with essential tools, and learn from experienced instructors through hands-on bootcamps and workshops.
In Summary
You’ll complete your stone faceting apprenticeship with extensive skills spanning equipment mastery, workspace setup, and precision cutting techniques. You’ve learned essential handpiece control, proper polishing methods, and accurate measurement protocols. Your training includes advanced mixed cuts, recutting expertise, and quality assessment abilities. You’ll continue developing through ongoing support resources, ensuring you’re equipped to create professionally faceted gemstones with confidence and precision throughout your career.
Leave a Reply