You’ll create stunning basse-taille effects by engraving intricate patterns into metal surfaces, then applying translucent enamels that transform your textures into luminous, dimensional artwork. Fire at temperatures between 750°C-850°C for 10-20 minutes, building thin layers to preserve underlying detail while achieving rich color saturation. The technique, dating to 13th-century Italy, produces spectacular depth as light plays through the glass surface, revealing your engraved patterns beneath. Master these fundamentals to access endless creative possibilities.
Understanding the Basse-Taille Technique and Its Historical Origins
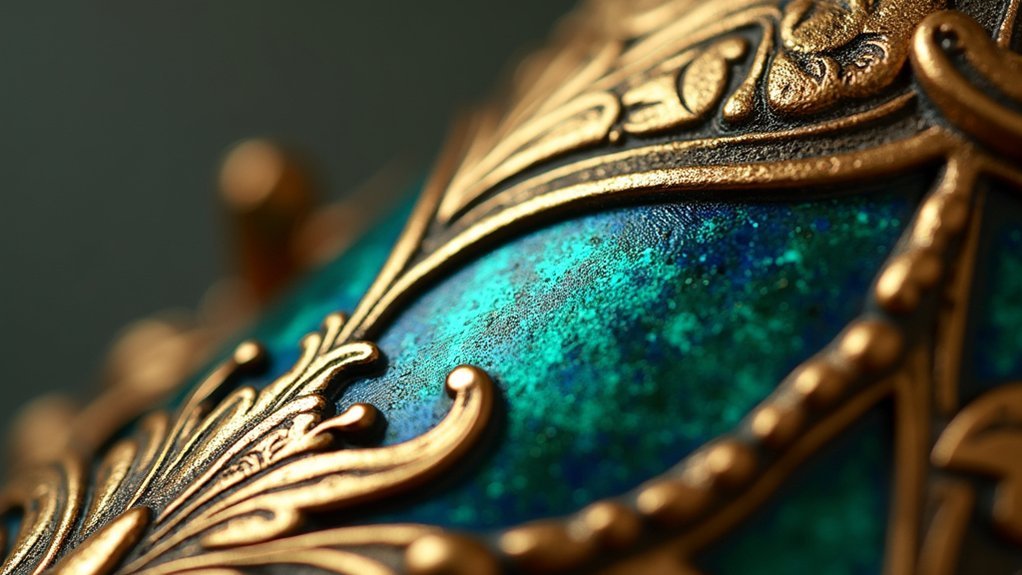
When you examine the intricate metalwork of medieval chalices or Renaissance jewelry, you’re likely witnessing the mastery of basse-taille, a sophisticated enameling technique that transforms simple engravings into luminous works of art.
This technique originated in late 13th-century Italy, with the earliest dated example being Guccio di Mannaia’s chalice for Pope Nicholas IV around 1290.
You’ll create basse-taille by engraving low-relief patterns into metal surfaces, typically gold or silver. The textured metal is then covered with translucent enamel, producing dramatic effects of light and shade through the interplay between carved surfaces and glass-like coating.
This technique gained prominence throughout Gothic and Renaissance Europe before experiencing a revival in 17th-century decorative arts.
Creating Textured Metal Surfaces for Enhanced Light Reflection
The foundation of exceptional basse-taille work lies in your ability to create precisely textured metal surfaces that will interact dramatically with translucent enamel. You’ll achieve stunning light reflection effects by engraving, chasing, or stamping shallow recesses into high-quality silver or gold. The depth variations you create directly influence how light passes through the colored glass and bounces back, producing enchanting visual dynamics.
Technique | Effect on Light Reflection |
---|---|
Engraving | Creates sharp linear patterns with distinct light play |
Chiseling | Produces varied depths for complex shadowing |
Engine-turning | Generates repetitive geometric textures |
Stamping | Forms consistent recessed patterns |
Your textured metal foundation must be meticulously prepared before applying finely ground glass enamel, ensuring the intricate design details shine through the translucent layer after firing.
Selecting and Preparing Translucent Enamels for Optimal Effects
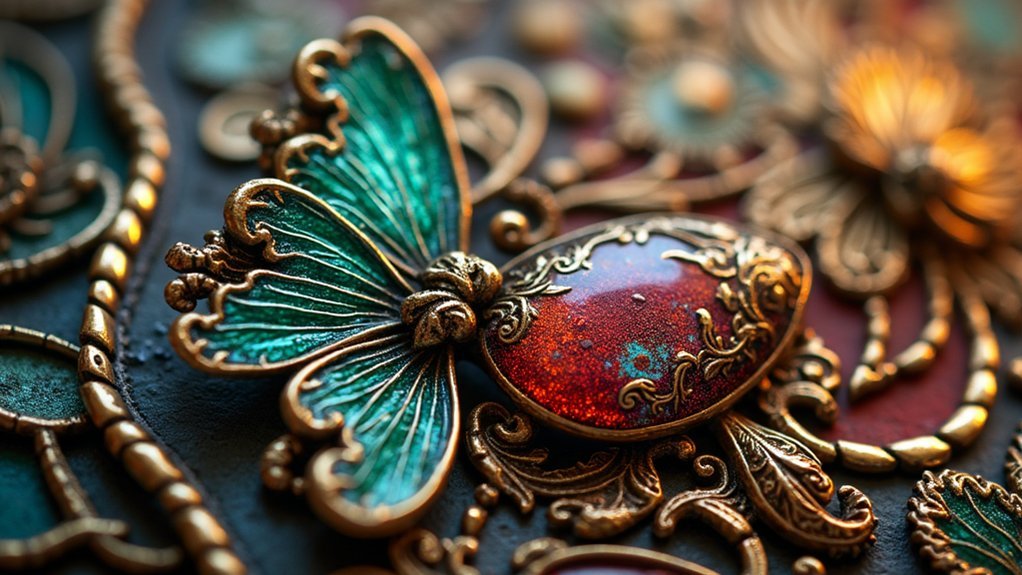
Three critical factors determine your success with translucent enamels: particle consistency, color selection, and proper medium preparation.
Start by carefully sieving your enamel powders to achieve uniform granulation—inconsistent particles create uneven fusion and compromise clarity.
Uniform particle size through careful sieving prevents uneven fusion and maintains the crystal-clear transparency essential for professional enamel work.
When selecting colors, light and transparent colors produce luminous effects that showcase the depths of the texture beneath, while darker shades enhance contrast and visual depth.
Your preparation and application process requires precise medium mixing to guarantee smooth application without air bubbles.
Master your firing temperatures and times since translucent enamels fuse at lower temperatures than opaque varieties.
Proper application techniques involve controlling layer thickness—thin, even coats preserve the underlying design’s visibility while building rich color saturation gradually.
Mastering Temperature Control and Firing Methods for Quality Results
You’ll achieve professional basse-taille results by maintaining precise firing temperatures between 750°C and 850°C, as even minor fluctuations can compromise your enamel’s clarity and color intensity.
Your kiln’s heat distribution patterns directly impact how evenly the enamel fuses to your prepared metal surface, making consistent temperature zones essential for uniform coverage.
Controlling your cooling rates prevents thermal shock that can crack or dull your finished work, so you must allow gradual temperature reduction rather than rapid cooling.
Optimal Firing Temperature Ranges
Achieving stunning basse-taille enamel effects hinges on mastering the critical temperature range of 750°C to 850°C (1382°F to 1562°F).
This ideal firing temperature guarantees proper fusion of enamel with your textured metal surface, creating the luminous depth characteristic of basse taille technique.
You’ll need precise control because exceeding this range causes bubbling or burning, while insufficient heat prevents proper adhesion.
Your firing times should typically span 10 to 20 minutes, depending on enamel thickness.
Use a programmable kiln controller for consistent results and even heating across your piece.
Before committing to final works, test small samples to fine-tune your temperature and timing parameters.
This experimentation prevents costly mistakes and helps you achieve superior enamel quality.
Kiln Heat Distribution Methods
While ideal firing temperatures provide the foundation for quality basse-taille work, mastering kiln heat distribution determines whether you’ll achieve consistent, professional results across your entire piece.
Uneven temperatures create color discrepancies and surface defects that’ll ruin your enamel finish.
Position kiln shelves strategically to promote proper airflow around your pieces during firing.
You’ll want to monitor kiln temperatures using thermocouples or pyrometers for accurate readings throughout the process.
Implement a preheating phase before reaching final temperatures – this enhances enamel adhesion to metal and prevents cracking.
Experiment with slow temperature ramping schedules to optimize enamel clarity and vibrancy.
These controlled firing methods guarantee even heat penetration, giving you the professional-grade results that showcase basse-taille’s distinctive translucent beauty.
Cooling Rate Control Techniques
Once your basse-taille piece reaches ideal firing temperature, controlling the cooling process becomes equally critical for preventing thermal shock and preserving enamel integrity.
You’ll want to maintain firing temperatures between 750°C to 850°C while implementing gradual cooling cycles that protect your work from cracking or bubbling.
Invest in kilns with programmable settings that allow precise cooling rate control throughout the entire process.
These systems enable you to experiment with different cooling speeds, creating unique effects that enhance your enamel’s depth and brilliance.
Slower cooling rates particularly help achieve peak enamel fusion while maintaining the clarity that showcases your underlying metalwork design.
Achieving Depth and Dimensional Effects Through Layered Applications
When you apply translucent enamel over carefully engraved recesses, you’ll create stunning dimensional effects that transform flat metalwork into visually dynamic pieces.
Your Basse-Taille Enamel technique relies on varying recess depths to control color intensity—deeper cuts produce richer, darker tones while shallow areas create lighter hues.
You’ll achieve maximum depth and dimension by building layers gradually. Start with thin applications of translucent vitreous enamel, firing between each layer.
This layering techniques approach allows light to penetrate multiple enamel layers and reflect off your textured metal base, creating extraordinary visual complexity.
Control your firing temperatures precisely to maintain enamel clarity. Each successive layer adds richness without obscuring underlying details.
You’re fundamentally painting with light itself, as the interplay between enamel thickness and metal texture creates colors that shift dramatically with viewing angles.
Modern Applications and Creative Variations in Contemporary Metalwork
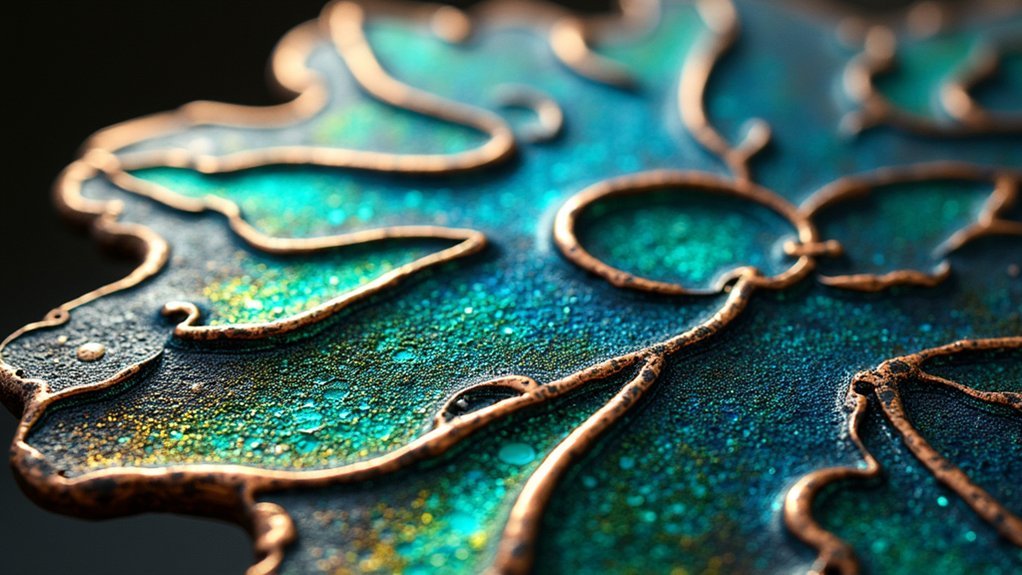
You’ll find today’s metalworkers pushing basse-taille beyond traditional boundaries through innovative approaches that blend historical techniques with cutting-edge technology.
Contemporary artists now integrate digital design software to create precise patterns before carving, while others combine basse-taille with unexpected materials like titanium or polymer clays.
These creative variations allow you to explore mixed media combinations that weren’t possible with classical methods, opening new avenues for artistic expression in modern metalwork.
Contemporary Artist Innovations
While traditional basse-taille techniques remain foundational, contemporary artists are revolutionizing this ancient craft by incorporating modern materials and innovative design approaches that push the boundaries of what’s possible in enameled metalwork.
You’ll discover that today’s metalworkers experiment with both opaque and translucent enamels, creating textural contrasts never seen in historical applications. Artists like Corina Gheorghe lead workshops teaching modern interpretations while preserving the technique’s integrity.
Innovation Area | Traditional Method | Contemporary Approach |
---|---|---|
Materials | Limited enamel types | Diverse opaque/translucent options |
Design Tools | Hand-carved patterns | Digital precision tools |
Technique Blending | Pure basse-taille | Mixed with cloisonné/champlevé |
Color Effects | Standard palette | Enhanced depth/color effects |
Creative Expression | Historical constraints | Unlimited aesthetic possibilities |
Digital tools now allow precise pattern design, while technique blending creates unprecedented artistic expressions in contemporary enamel effects.
Digital Design Integration
As digital technology transforms traditional metalworking, you’re witnessing a revolutionary fusion where computer-aided design meets centuries-old basse-taille techniques.
You can now create intricate patterns using software that guarantees precise engraving processes, producing complex textures that enhance your enamel effects dramatically. When you integrate laser engraving with traditional basse taille methods, you’ll achieve unprecedented precision and detail impossible with manual tools alone.
Contemporary artists are pushing boundaries by experimenting with digital color mixing and layering, creating innovative enamel effects that redefine traditional aesthetics.
You’ll find that 3D printing creates perfect templates and molds for your projects, streamlining production while preserving artistic integrity. This digital design integration allows you to customize and reproduce your metalwork with remarkable consistency and creativity.
Mixed Media Combinations
Three distinct approaches define how contemporary metalworkers integrate basse-taille enameling with mixed media elements.
You’ll discover transformative possibilities when combining traditional enameling with modern materials and techniques.
Contemporary artists are revolutionizing basse-taille through these innovative combinations:
- Wood and resin fusion – Creates stunning contrasts between organic textures and glossy colored glass surfaces
- Laser-engraved precision – Delivers intricate details that weren’t possible with traditional hand-engraving methods
- Cloisonné partnerships – Expands your color palette while adding complex visual storytelling elements
- Patination contrasts – Produces dramatic effects between aged, textured metal and brilliant enamel finishes
- Large-scale installations – Challenges conventional boundaries by incorporating traditional techniques into ambitious mixed media artworks
You’re witnessing a renaissance where ancient basse-taille techniques merge seamlessly with contemporary materials, creating pieces that honor tradition while embracing innovation.
Frequently Asked Questions
What Happens When Enamel Is Applied to Metals?
When you apply enamel to metals, you’re fusing glass paste to the surface during firing. This creates a durable, vibrant coating that transforms the metal’s appearance and provides lasting protection against wear.
What Is a Basse Taille Art?
You’ll find basse-taille is an enameling technique where you engrave shallow designs into metal, then apply translucent enamel over them, creating stunning depth and light effects through color variations.
Which of the Enameling Techniques Is the Most Difficult?
You’ll find basse-taille is widely considered the most difficult enameling technique. You’re required to master precise engraving, perfect translucent enamel application, and exact temperature control while understanding complex light interactions.
Which Metal Is More Preferred for Enameling Process and Why?
You’ll find silver’s most preferred for enameling because it’s got excellent thermal conductivity, ensuring even heat distribution during firing. It doesn’t react with enamels and provides beautiful, consistent results every time.
In Summary
You’ve now explored the intricate world of basse-taille enamel, from its historical roots to modern innovations. By mastering textured surfaces, selecting quality translucent enamels, and controlling firing temperatures, you’ll create stunning dimensional effects that capture and reflect light beautifully. Remember that layering techniques are key to achieving depth, while contemporary applications offer endless creative possibilities. Practice these methods consistently, and you’ll develop the expertise needed to produce truly spectacular basse-taille enamel work in your metalwork projects.
Leave a Reply