Industrial stone cutting uses advanced machinery and diamond drill bits to mass-produce identical pieces with ±0.01mm precision tolerances, while artisanal cutting relies on hand tools and traditional techniques that require years of mastery. You’ll find industrial methods prioritize speed, consistency, and cost-effectiveness, whereas artisanal approaches emphasize unique craftsmanship and individual character. Industrial stones cost less due to automation, but handcrafted pieces command premium prices for their distinctive artistry and time-intensive creation process that reveals deeper complexities.
Understanding Industrial Stone Cutting Methods
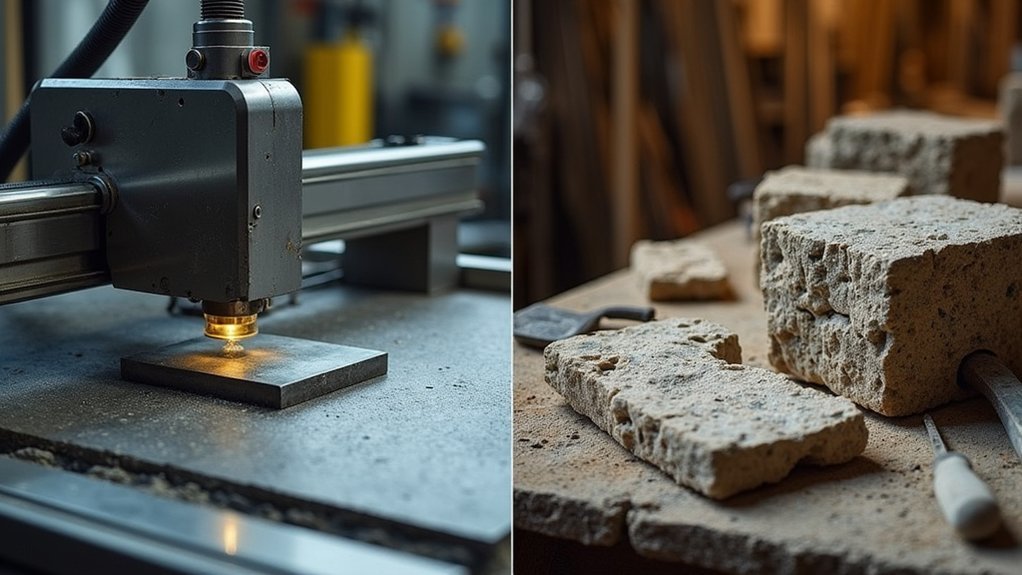
When you examine industrial stone cutting methods, you’ll discover they rely on cutting-edge technology that transforms raw materials into precisely crafted gems.
Industrial-grade diamond drill bits create cleaner, sharper facets than traditional artisanal techniques can achieve. You’ll find these methods enable mass production of identical stone beads with consistent precision cut quality at lower price points.
Industrial diamond cutting technology delivers superior facet precision and enables cost-effective mass production of uniformly crafted stone beads.
The process employs geometric principles tailored to specific stone types, ensuring facets remain nearly perfectly flat while minimizing polishing requirements.
You can see this technology’s impact in extremely small beads that maintain high luster, enhancing sparkle even in stones like jasper.
Specialized machinery delivers greater efficiency and uniformity throughout production, contrasting sharply with hand-crafted artisanal methods that typically show significant variability.
The Art of Artisanal Stone Cutting Techniques
You’ll discover that artisanal stone cutting relies on hand-carved precision methods that can’t be replicated by machines.
Your success depends on mastering traditional tools like jam pegs and handpiece machines, which require years of experience to handle properly.
When you embrace these techniques, you’ll create unique patterns that showcase each stone’s individual character and natural beauty.
Hand-Carved Precision Methods
Three fundamental elements distinguish hand-carved precision methods from industrial stone cutting: the artisan’s intimate relationship with the material, the deliberate pace that allows for creative expression, and the irreplaceable human touch that breathes life into each piece.
When you choose hand-carved stonework, you’re investing in traditional techniques that emphasize chiseling and polishing over mechanical precision. Each artisan carefully studies your stone’s natural properties, working with—not against—its inherent characteristics to enhance beauty while preserving integrity.
You’ll notice how manual methods create intricate designs and personalized touches that machines can’t replicate. This time-intensive process means you’re paying premium costs, as artisans often spend weeks or months perfecting single pieces.
The result? Stone pieces showcasing natural variations and distinct character that reflects individual craftsmanship.
Traditional Tool Mastery
Although modern machinery dominates today’s stone industry, traditional tool mastery remains the cornerstone of authentic artisanal craftsmanship. You’ll discover that mastering hand chisels and hammers requires years of dedicated practice and deep understanding of stone properties. This expertise enables you to execute precise cuts and intricate details that machinery simply can’t replicate.
Traditional Tool | Skill Development Time | Unique Capability |
---|---|---|
Hand Chisels | 3-5 years | Detailed surface texturing |
Stone Hammers | 2-4 years | Controlled fracturing |
Pneumatic Tools | 1-2 years | Rapid rough shaping |
Measuring Calipers | 6 months | Precision dimensioning |
Finishing Files | 1-2 years | Surface smoothing |
When you embrace these time-honored techniques, you’re preserving cultural heritage while creating pieces that showcase natural stone variations and your personal artistic vision.
Unique Pattern Creation
When you move beyond traditional tool mastery into unique pattern creation, you’re entering the domain where artisanal stone cutting truly distinguishes itself from industrial methods.
You’ll discover that each piece becomes a canvas where natural variations in color and veining guide your creative decisions. Unlike mass production’s uniform results, you’re crafting one-of-a-kind designs that celebrate stone’s inherent character.
Your patterns can incorporate cultural influences and historical styles, creating pieces that tell stories beyond mere decoration.
You’ll embrace irregularities and imperfections as features rather than flaws, understanding they contribute to authenticity. This approach allows you to produce bespoke pieces that clients value precisely because they can’t be replicated through industrial processes.
Machinery and Equipment: Mass Production Vs Hand Tools
You’ll find that industrial stone cutting machines deliver precision tolerances as fine as ±0.01 mm, while hand tools offer the flexibility to create unique artistic variations that machines can’t replicate.
Mass production equipment cuts gemstones at high speeds with consistent results, but you’re trading that efficiency for the personalized touch that skilled artisans achieve with traditional tools.
The equipment you choose fundamentally determines whether you’re producing uniform stones quickly or crafting distinctive pieces that showcase individual craftsmanship.
Machine Precision Capabilities
Since industrial stone cutting harnesses advanced machinery like computer-controlled tools and mass production equipment, you’ll notice dramatically different precision capabilities compared to traditional artisanal methods.
Industrial-grade diamond drill bits create cleaner, sharper facets while enabling faster production speeds.
When you compare machine-cut versus hand-cut stones, you’ll find these key differences:
- Facet Quality: Machine-produced gemstone beads feature nearly perfectly flat facets that enhance sparkle.
- Consistency: Advanced machinery delivers identical specifications across large quantities.
- Finishing Requirements: Precision-cut stones need minimal polishing compared to extensive hand-finishing.
- Production Speed: Computer-controlled tools operate markedly faster than traditional hand methods.
You’re getting superior consistency and reduced finishing time with industrial precision, while artisanal methods produce unique variations reflecting individual craftsmanship and style.
Hand Tool Flexibility
Hand tools offer artisans remarkable flexibility that mass production machinery simply can’t match. You’ll find that artisans can adapt their techniques on-the-fly, making real-time adjustments based on each stone’s unique characteristics. This adaptability enables intricate designs, unique shapes, and personalized finishes that reflect individual creativity and skill.
Aspect | Hand Tools | Mass Production |
---|---|---|
Adaptability | Real-time technique adjustments | Fixed automated processes |
Output | One-of-a-kind pieces with character | Identical uniform products |
Design Freedom | Intricate, personalized creations | Geometric, standardized cuts |
While industrial diamond drill bits produce cleaner facets at lower costs, your hand tool methods create depth and character that mass production can’t replicate. The cutter’s experience and craftsmanship drive quality variations, whereas industrial precision relies on geometric calculations and automation for consistent uniformity.
Production Speed Differences
When comparing production speeds, industrial stone cutting machinery operates at dramatically different rates than traditional hand tools.
You’ll find that mass machines can produce hundreds of identical pieces while an artisan completes just one hand-cut stone.
Industrial-grade diamond drill bits create cleaner facets with remarkable efficiency, whereas hand tools require meticulous attention that considerably extends completion time.
Here’s what affects production speed differences:
- Volume capacity – Mass machines handle bulk production versus single-piece crafting
- Automation level – Industrial processes run continuously while hand cutting requires constant manual input
- Precision tools – Advanced equipment cuts faster than traditional implements
- Quality consistency – Machines maintain uniform standards without the variability of handwork
You’ll pay less for industrial stones due to this speed advantage, but artisanal pieces offer unique character.
Quality Control Standards in Different Cutting Approaches
Although both industrial and artisanal stone cutting produce finished gems, their quality control standards differ dramatically in approach and execution.
When you choose industrial cutting, you’ll get standardized precision with tolerances of plus or minus 0.01 mm. Mass machines guarantee uniformity across large production runs, creating consistent quality control through set parameters.
However, if you select artisanal cutting, you’re relying on individual craftsmen’s expertise rather than strict metrics. Each skilled gem cutter assesses stones individually, leading to unique variations based on their experience and techniques.
While this creates less standardized results, you’ll often receive higher-quality stones with personalized characteristics.
Industrial methods prioritize consistency and cost-effectiveness, whereas artisanal approaches emphasize craftsmanship and uniqueness, resulting in premium products that command higher prices.
Time Investment and Production Speed Comparisons
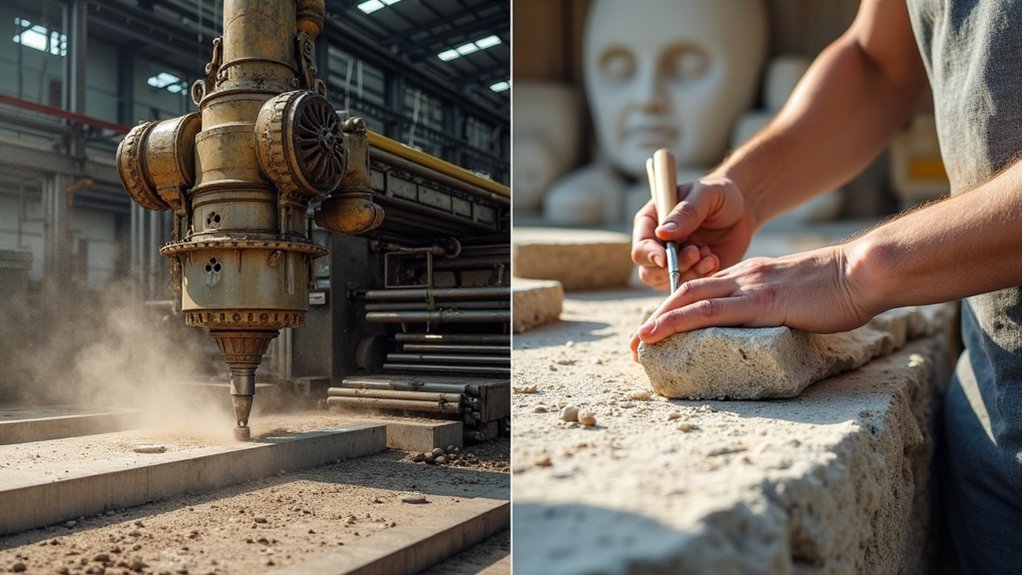
Production speed represents one of the most striking differences between industrial and artisanal stone cutting methods. When you’re choosing between these approaches, you’ll notice dramatically different timeframes and investment requirements.
Industrial cutting leverages advanced machinery and diamond drill bits to produce thousands of identical pieces rapidly. You can expect mass production that’s cost-effective due to economies of scale.
Conversely, artisanal cutting demands extensive time investment, with individual stones requiring days or weeks to complete.
Here’s what impacts your production timeline:
- Machine efficiency – Industrial equipment streamlines processes considerably
- Labor intensity – Artisanal methods require meticulous handcrafting attention
- Design complexity – Bespoke creations take considerably longer than uniform cuts
- Volume capacity – Industrial processes handle massive quantities simultaneously
This speed difference directly affects pricing and availability.
Cost Factors Between Industrial and Handcrafted Methods
Since economics drive most purchasing decisions, understanding the cost differences between industrial and handcrafted stone cutting becomes essential for your project planning.
Industrial methods greatly reduce your costs through mass production and economies of scale. You’ll find diamond drill bits and automated machinery create uniform pieces efficiently, minimizing labor expenses and polishing requirements.
Conversely, you’ll pay premium prices for artisanal stones due to their labor-intensive nature and limited production volumes. Handcrafted pieces require skilled artisans who invest considerable time in individual stones, extensive polishing, and finishing work.
The price disparity can be substantial, with artisanal stones commanding higher costs that reflect their unique characteristics and artistry. Your choice ultimately depends on balancing budget constraints against desired quality and exclusivity.
Skill Requirements and Training for Each Approach
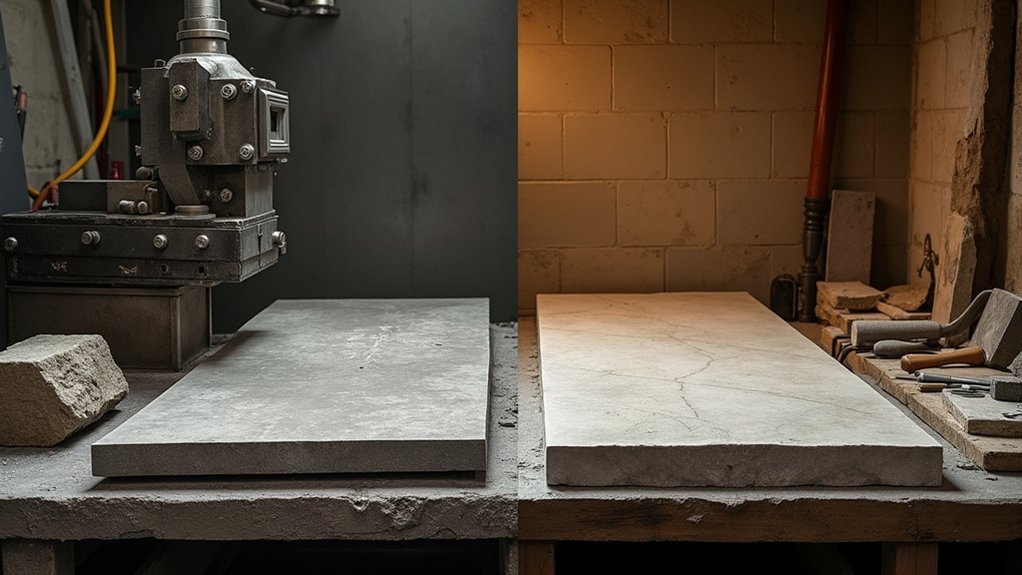
While economic considerations shape your initial decisions, the skill requirements and training pathways for each approach differ dramatically in scope and duration.
If you’re pursuing industrial stone cutting, you’ll focus on machine operation and maintenance through shorter training programs that emphasize speed and consistency.
However, artisanal cutting demands years of apprenticeship where you’ll develop:
- Hand technique mastery – Complex geometric shapes and precise faceting skills
- Material expertise – Deep understanding of stone properties and behaviors
- Artistic vision – Creative problem-solving and individual expression capabilities
- Continuous learning – Ongoing education in evolving design trends and techniques
You’ll find that artisanal work prioritizes craftsmanship and creativity, while industrial methods focus on standardization and volume output through advanced machinery operation.
Precision and Consistency in Stone Cutting Results
These distinct skill development paths directly impact the precision and consistency you’ll achieve in your final products.
Industrial-grade diamond drill bits utilize advanced technology to create cleaner, sharper facets, delivering more consistent quality than artisanal methods that vary considerably. You’ll find precision cut gemstones designed using geometric principles optimize cuts for enhanced sparkle while requiring less polishing, achieving higher consistency than traditional hand-cutting.
Mass production lets you create identical stone beads through automated processes, while artisanal cutting depends on individual skill and experience, creating variations in quality and finish.
Industrial precision allows you to produce extremely small beads with high luster consistently—something that’s challenging with hand-cutting. While artisanal methods offer unique characteristics, industrial techniques prioritize uniformity and repeatability, ensuring each piece meets specific standards.
Market Value and Consumer Preferences
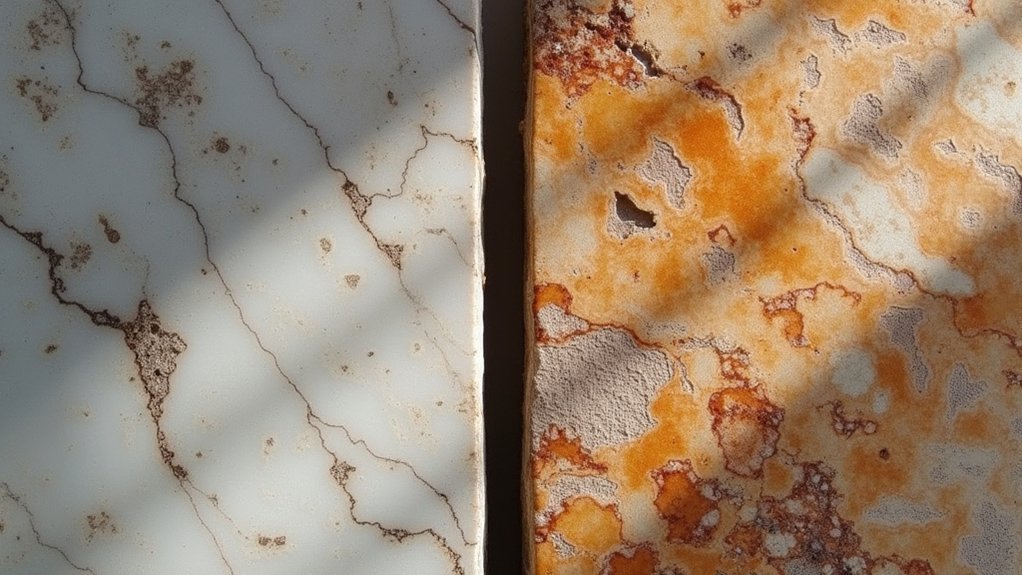
Two distinct market segments emerge when examining consumer preferences for stone cutting methods, each driven by different value propositions and purchasing motivations.
If you’re budget-conscious or need uniformity for mass production, you’ll likely prefer industrial-grade diamond drill bits that deliver consistent, precise cuts at lower prices.
However, if you value craftsmanship and uniqueness, artisanal cutting offers one-of-a-kind pieces that command higher market values.
Artisanal stone cutting commands premium prices by delivering distinctive, handcrafted pieces that mass production simply cannot replicate.
Consumer preferences are shifting toward artisanal methods due to:
- Growing demand for sustainable and ethically sourced materials
- Preference for environmentally friendly cutting practices
- Desire for bespoke, customized stone pieces
- Willingness to pay premiums for personalized, distinctive items
You’ll find precision-cut gemstone beads with advanced geometry appeal when seeking enhanced sparkle and eye-catching jewelry pieces.
Choosing the Right Cutting Method for Your Project
How do you determine which cutting method will best serve your specific stone project? Start by considering your project’s scope and budget. Industrial-grade diamond drill bits excel when you need mass production of identical pieces at lower costs, creating cleaner, more intricate facets perfect for large-scale operations.
For smaller projects requiring detailed work, precision cut gemstone beads offer superior sparkle through ideal geometric cuts. Consider your stone’s specific properties—precision cuts can dramatically enhance even unconventional stones like jasper.
Factor | Industrial Method | Artisanal Method |
---|---|---|
Cost | Lower per unit | Higher per piece |
Uniqueness | Uniform results | One-of-a-kind patterns |
Production Volume | Mass production | Small batches |
Detail Level | Consistent precision | Custom intricacy |
Best For | Commercial projects | Custom jewelry |
Frequently Asked Questions
What Is Someone Who Cuts Stones Called?
You’d call someone who cuts stones a “gem cutter” or “lapidary.” They’re specialists who shape and polish gemstones, working with precious and semi-precious stones to enhance their natural beauty for jewelry.
What Is the Process of Stone Cutting?
You’ll start by selecting raw stone, then extract and roughly shape it using appropriate tools. Next, you’ll refine the shape through careful cutting, followed by polishing and quality inspection to guarantee proper craftsmanship standards.
How Much Does Stone Cutting Cost?
You’ll spend $5-$50 per piece for industrial stone cutting, while artisanal work costs $50-several hundred dollars each. Your final price depends on stone type, cut complexity, and whether you choose machine or hand cutting methods.
What Is Stone Cutting Called?
You’ll find stone cutting called “lapidary” or “gem cutting.” These terms describe the craft of shaping and polishing stones. You might also hear “faceting” for precise cuts or “cabochon cutting” for smooth, rounded finishes.
In Summary
You’ll find that choosing between industrial and artisanal stone cutting depends on your project’s specific needs. If you’re prioritizing speed, consistency, and cost-effectiveness for large volumes, industrial methods are your best bet. However, if you value unique character, traditional craftsmanship, and don’t mind investing more time and money, artisanal techniques will deliver exceptional results. Consider your budget, timeline, and desired aesthetic when making your decision.
Leave a Reply