Choosing the right lapidary wheel directly impacts your stone’s final quality and your equipment’s longevity. You’ll need different materials like diamond, resin, or silicon carbide wheels depending on your project’s requirements. Proper grit selection guarantees efficient material removal and smooth finishes, while matching wheel hardness to your stone type prevents damage. Wrong wheel choices can crack delicate stones, create uneven surfaces, or cause excessive wear on your machinery. Understanding these fundamentals will transform your lapidary results.
Understanding Different Lapidary Wheel Materials
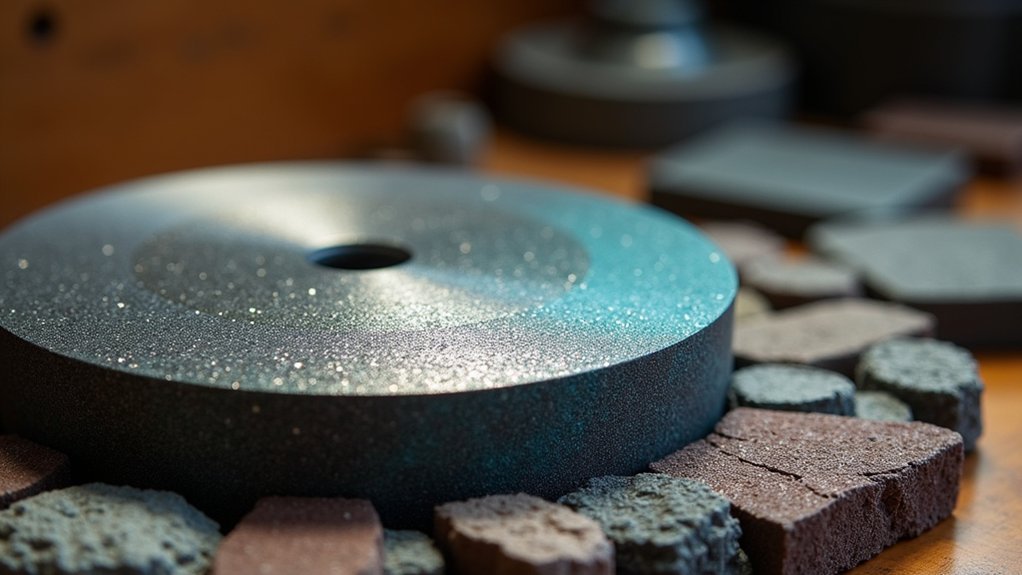
When selecting a lapidary wheel, you’ll encounter five primary material types, each engineered for specific stages of stone working.
Diamond wheels come in three distinct varieties: resin-bonded wheels provide flexible surfaces perfect for smoothing and pre-polishing with premium binders extending their lifespan.
Resin-bonded diamond wheels deliver flexible smoothing capabilities with premium binders that significantly extend operational lifespan for pre-polishing applications.
Electroplated versions feature hard backings for aggressive shaping, incorporating textured surfaces that facilitate sediment washout.
Sintered diamond wheels offer exceptional cost-effectiveness and longevity through concentrated diamond content, delivering balanced operation for heavy-duty applications.
Silicon carbide presents an economical alternative for general shaping tasks, appealing to budget-conscious lapidaries.
Finally, specialized cork and felt wheels handle glass polishing exclusively—cork wheels create hazy finishes with pumice while felt wheels achieve optical clarity using cerium.
Grit Size Selection for Optimal Performance
After determining your wheel material, grit size becomes the determining factor in your stone’s final appearance and the efficiency of your work process.
You’ll want to start with coarser grits like 220 for aggressive shaping, then progress through finer grits for polishing. The right equipment sequence begins with 80 and 220 grit wheels, advancing through 140, 280, 600, 1200, and 3000 grits.
- Coarse grits (80-220): Best for initial shaping and removing material quickly from harder stones
- Medium grits (280-600): Ideal for refining shapes and smoothing surfaces before final polishing
- Fine grits (1200-3000): Perfect for achieving mirror-like finishes on diamond and precious stones
Remember that grit sizes below 200 often prove less effective, making 220 your go-to choice for delicate materials.
Resin and REZ Wheels for Smooth Finishing
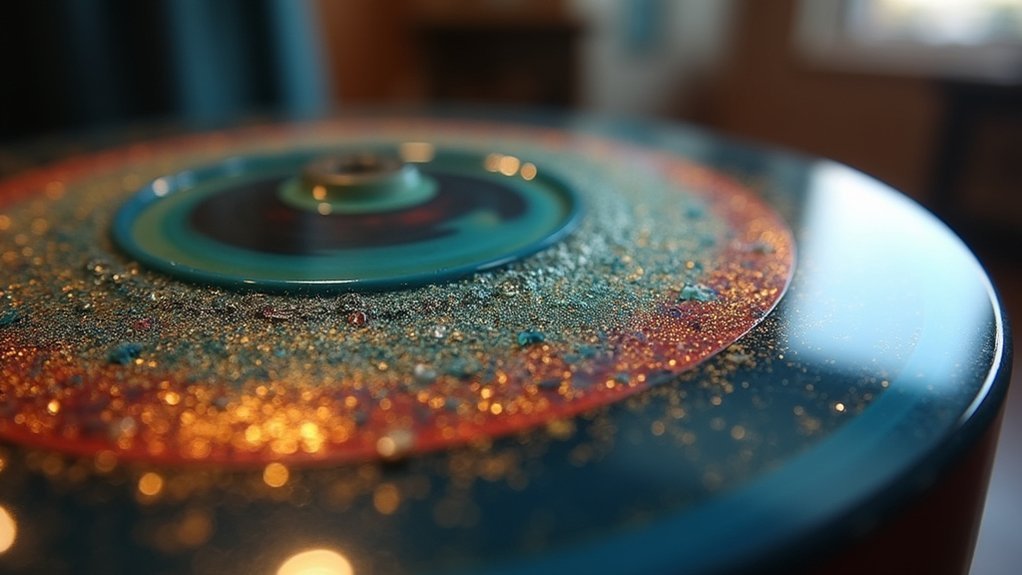
Once you’ve selected your grit sequence, diamond resin wheels become your go-to choice for achieving those smooth, professional finishes that separate amateur work from expert cabochons.
These wheels feature soft backing that provides flexibility for contour smoothing, making them forgiving on softer curves and ideal for pre-polishing work.
You’ll find resin wheels particularly effective at removing flat spots and high spots during cabbing. Their soft construction works brilliantly on expanding drum systems, conforming to various stone shapes.
Diamond REZ wheels offer premium resin binders for longer life and slightly more aggressive cutting, though they’ll need a small break-in period.
Coarser grits like 220 work exceptionally well with resin wheels, efficiently preparing your stones for final polishing stages.
Electroplated Diamond Wheels for Precision Shaping
While resin wheels excel at smooth finishing work, electroplated diamond wheels deliver the aggressive cutting power you need for precision shaping tasks.
Their hard backing provides the inflexible support necessary for detailed work, making them perfect for cabbing and intricate stone shaping projects.
The nickel-bonded diamond surface guarantees smooth operation while removing material effectively.
Many electroplated wheels feature a textured cross-hatch design that helps wash away sediment during use, maintaining peak performance throughout your project.
Key advantages of electroplated diamond wheels include:
- Aggressive cutting power – More aggressive than standard diamond wheels for demanding applications
- Precision capability – Hard backing enables detailed shaping work requiring high accuracy
- Efficient operation – Cross-hatch texture facilitates sediment washout for consistent performance
Choose electroplated wheels when your project demands both aggressive material removal and precise control.
Sintered Diamond Wheels for Heavy-Duty Applications
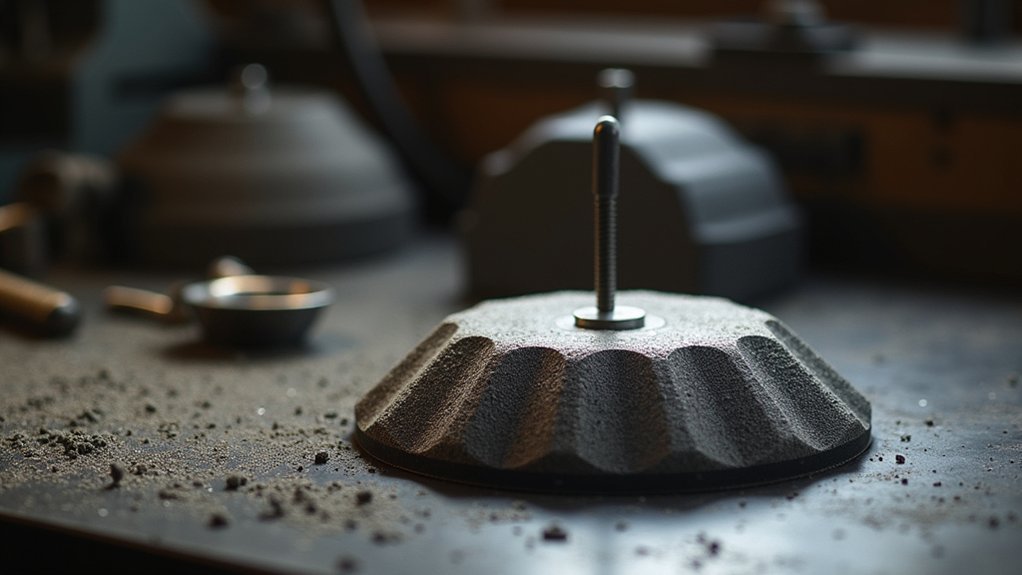
When you’re tackling demanding lapidary projects that require aggressive material removal, sintered diamond wheels deliver the heavy-duty performance you need with their superior diamond concentration of over 3/16 inch throughout the wheel.
You’ll find these wheels maintain consistent grinding efficiency longer than standard alternatives, making them a cost-effective long-term investment despite their higher upfront cost.
Their evenly dispersed diamond particles through the sintering process guarantee you can remove significant amounts of hard material while still achieving smooth finishes.
Cost-Effective Long-Term Investment
Many lapidary enthusiasts discover that sintered diamond wheels represent the most cost-effective choice for heavy-duty grinding applications.
You’ll find these wheels outlast other diamond wheel types considerably, minimizing replacement costs over time. The Ultimate Sintered Diamond Wheel by Covington contains over 3/16 inch of concentrated diamond, ensuring robust performance that handles tough materials without frequent replacements.
When you invest in sintered diamond wheels, you’re choosing durability that translates to real savings:
- Extended lifespan – Outlasts other diamond wheel types through proper maintenance
- Consistent performance – Even diamond dispersion provides balanced operation across various materials
- Reduced replacement frequency – Handles extensive grinding tasks without premature wear
Their long-lasting performance makes them a wise investment for serious lapidary work, delivering exceptional value through sustained effectiveness.
Superior Diamond Concentration Benefits
Because sintered diamond wheels contain over 3/16 inch of concentrated diamond material, they deliver unmatched cutting power for demanding lapidary applications.
You’ll experience superior performance when working with tough materials that would quickly wear down standard wheels. The even diamond dispersion achieved through sintering guarantees balanced operation throughout your grinding sessions, eliminating hot spots and vibrations that compromise precision.
This concentrated diamond construction means you can tackle heavy-duty shaping and polishing tasks with confidence.
You’ll maintain consistent results even under high pressure and heat conditions. The robust design withstands intensive use while delivering the cutting efficiency you need for challenging projects.
When you’re working with particularly difficult materials, this superior diamond concentration translates directly into better performance and professional-quality results.
Heavy-Duty Grinding Performance
Sintered diamond wheels excel in heavy-duty grinding scenarios where standard wheels fail to deliver adequate performance. When you’re tackling demanding lapidary projects, these wheels deliver the aggressive grinding power you need while maintaining exceptional durability.
Their robust construction withstands intense pressure and heat, allowing you to shape and finish hard materials efficiently without compromising wheel integrity.
The concentrated diamond content guarantees you’ll achieve consistent results across extended grinding sessions.
You’ll find these wheels particularly valuable for:
- Extended grinding operations – Outlasting conventional wheels through superior wear resistance
- High-pressure applications – Maintaining structural integrity under demanding conditions
- Cost-effective performance – Reducing replacement frequency and downtime costs
With proper maintenance, you’ll maximize both productivity and tool longevity in your heaviest grinding tasks.
Silicon Carbide Wheels for Budget-Conscious Crafters
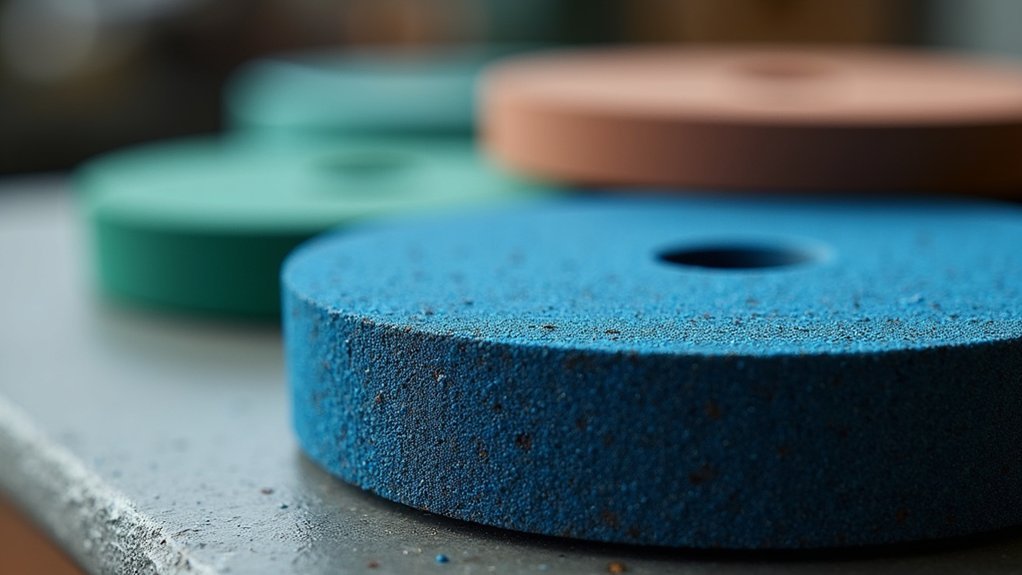
If you’re working within a tight budget, silicon carbide wheels offer an excellent entry point into lapidary work without breaking the bank.
You’ll find these cost-effective wheels deliver solid performance for general stone shaping and grinding tasks, making them perfect for beginners or hobbyists who don’t want to invest heavily upfront.
They’re widely available and often come bundled with grinder units, giving you immediate access to essential lapidary capabilities while you build your skills and determine your long-term tool needs.
Cost-Effective Stone Shaping
Three key factors make silicon carbide wheels an excellent choice for budget-conscious lapidary enthusiasts: affordability, versatility, and reliable performance.
You’ll find these wheels commonly included with grinder combos, providing an economical alternative to expensive diamond wheels without sacrificing effectiveness for general shaping tasks.
These wheels deliver impressive value by handling everything from rough shaping to finer finishing work. You can experiment with various lapidary projects without significant financial investment, making them perfect for beginners and hobbyists.
Key advantages of silicon carbide wheels include:
- Cost-effective pricing that won’t strain your crafting budget
- Versatile performance across multiple stone-working applications
- Durable construction offering reliable results for extended use
You’ll achieve satisfactory outcomes while keeping expenses manageable, allowing you to focus on developing your lapidary skills.
Economic Alternative Benefits
When you’re starting your lapidary journey or working within a tight budget, silicon carbide wheels deliver exceptional value that extends far beyond their initial purchase price.
You’ll find these wheels commonly included with many grinders and combos, giving you immediate versatility for various applications without additional costs. They’re built to withstand regular use, ensuring you won’t need frequent replacements that drain your budget.
These wheels effectively handle general shaping tasks, letting you achieve satisfactory results without investing in expensive diamond alternatives.
Cork and Felt Wheels for Glass Polishing
While standard lapidary wheels excel at shaping and grinding, cork and felt wheels serve specialized roles in glass polishing that you can’t achieve with conventional abrasives.
You’ll find cork wheels work perfectly with pumice to create hazy, textured finishes that enhance your glass surfaces. For crystal-clear results, felt wheels paired with cerium oxide deliver exceptional optical finishes with brilliant shine.
These wheels offer distinct advantages for glass work:
- Versatile sizing options – Choose from various wheel sizes to match your specific glass applications and desired finish quality
- Durable construction – Dense cork and felt materials withstand repeated use while maintaining consistent polishing performance
- Specialized compatibility – Engineered specifically for glass materials, delivering superior results compared to standard polishing methods
Both options provide reliable, professional-grade finishes for your glasswork projects.
Hard Vs Soft Wheel Backing Options
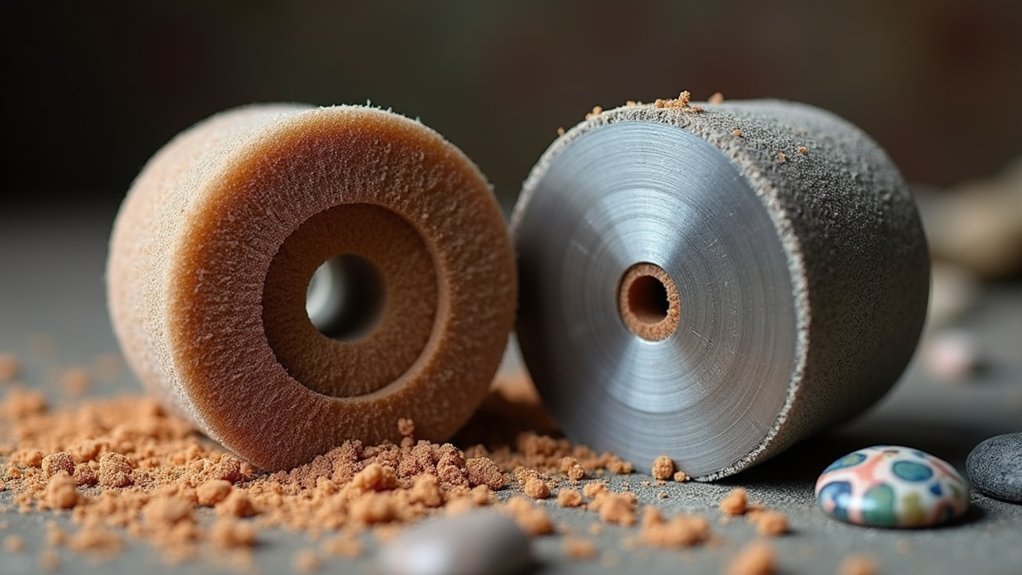
Your wheel’s backing material determines how it performs across different lapidary tasks and stone types. Hard backings, found in electroplated diamond wheels, deliver aggressive grinding that’s perfect for shaping projects but lack the flexibility needed for softer materials. Soft backings, like those in diamond resin wheels, conform to your stone’s shape, enabling efficient smoothing and pre-polishing while preventing flaking on delicate materials.
Backing Type | Best For | Grit Usage |
---|---|---|
Hard | Tough materials, aggressive shaping | Various grits for shaping |
Soft | Softer stones, smoothing | 220 for shaping, fine for finishing |
Soft | Curved surfaces, eliminating flat spots | Fine grits for polishing |
Choose soft wheels for softer stones to prevent damage, while hard wheels excel at shaping tougher materials effectively.
Wheel Size Compatibility With Your Equipment
Beyond selecting the right backing material, wheel size plays a major role in how well your lapidary equipment performs. You can use 6-inch wheels on 8-inch machines, but you’ll need to verify compatibility with wheel covers and water feeds first.
Smaller wheels create water splashing issues that require adjusting your water feed placement for ideal performance.
The size difference greatly impacts your cutting efficiency:
- Surface Area: 6-inch wheels offer less cutting surface than 8-inch wheels, resulting in longer cutting times.
- Rim Speed: Larger wheels provide higher rim speeds, enabling faster and easier cutting operations.
- Contact Quality: Proper wheel-to-workpiece contact maximizes cutting efficiency and minimizes premature wear.
Choose wheel sizes that match your machine’s specifications to guarantee effective operation and maintain cutting performance standards.
Matching Wheel Types to Stone Hardness
Since stone hardness determines how aggressively you can cut without damaging your material, selecting the right wheel type becomes critical for achieving professional results.
You’ll need softer wheels with coarser grits like 220 for delicate stones, allowing aggressive shaping without causing damage. For harder materials, electroplated diamond wheels provide the aggressive cutting power you need, while sintered diamond wheels offer excellent longevity and balanced performance across various hardness levels.
Silicon carbide wheels work perfectly for general shaping of softer stones without diamond wheels’ higher costs.
Understanding your specific stone’s hardness directly affects both efficiency and quality of your work. You can’t achieve peak results without matching wheel characteristics to material properties, as this pairing determines cutting speed and surface finish quality.
Water Feed Requirements for Different Wheels
Water feed systems require specific adjustments based on your wheel size to maintain ideal cutting performance and prevent overheating.
You’ll need to guarantee proper contact with the cutting face of your wheel, as inadequate water flow leads to overheating and reduced efficiency.
When you’re using smaller wheels like 6-inch varieties, focus your water feed more precisely to prevent splashing and maintain consistent lubrication.
Larger 8-inch wheels offer more surface area, providing better water distribution that enhances cutting performance and minimizes sediment buildup.
Key water feed considerations include:
- Adjusting feed placement to ensure water adequately reaches the cutting surface
- Focusing water streams more precisely on smaller wheels to prevent waste
- Taking advantage of larger wheels’ superior water distribution capabilities
Wheel Maintenance and Longevity Factors
While proper water flow keeps your wheels running smoothly during operation, maintaining their condition between uses determines how long they’ll serve you effectively.
You’ll need to clean your wheels regularly to prevent sediment and debris buildup that damages performance. Store them away from moisture and direct sunlight to avoid deterioration.
Match the right grit to your materials—this prevents unnecessary wear and maintains cutting efficiency. Always follow manufacturer guidelines for operational speeds and pressure to prevent premature damage.
You should inspect your wheels periodically for cracks or uneven surfaces. These warning signs indicate it’s time for maintenance or replacement before your cutting results suffer.
Proper maintenance practices will considerably extend your wheels’ lifespan and preserve their ideal performance.
Frequently Asked Questions
How to Choose the Right Grinding Wheel?
You’ll need to match the wheel’s hardness to your material – soft wheels for softer stones, diamond wheels for harder ones. Consider grit size, backing type, and guarantee compatibility with your machine specifications.
What Are the Various Factors to Be Considered for Selection of a Grinding Wheel?
You’ll need to contemplate material composition, grit size, wheel hardness, machine compatibility, and backing type. These factors determine cutting efficiency, surface finish quality, and overall grinding performance for your specific application.
Which Grinding Wheel Characteristic Determines the Wheel’s Grade?
You’ll find that grit size primarily determines a grinding wheel’s grade. Coarser grits create aggressive cutting action for shaping, while finer grits provide smoother finishes for polishing your lapidary projects.
Are Diamond Grinding Wheels Worth It?
You’ll find diamond grinding wheels absolutely worth the investment. They’ll last longer, cut more efficiently, and produce superior finishes on gemstones while reducing material damage compared to traditional wheels.
In Summary
You’ll achieve better results and save money when you select the right lapidary wheel for your specific project. Don’t compromise on quality or compatibility – match your wheel’s material, grit, and size to your stone’s hardness and your equipment’s specifications. Remember that proper water feed and regular maintenance will extend your wheel’s life considerably. Take time to understand these factors, and you’ll transform rough stones into polished gems more efficiently and effectively.
Leave a Reply